Sealing Cell Module Controllers Using the CIPG Process
Battery sensors play a crucial role in controlling and managing the performance and safety of electric vehicle batteries. They monitor parameters such as temperature, voltage, and current, and report this information to the battery management system (BMS), which controls and monitors the battery's charging and discharging processes.
Read more aboutNew B8650 impregnation machine for sustainable impregnation of electrical motors
The release of the B8650 impregnation machine enhances the electrical component manufacturing, specifically targeting the impregnation of windings in rotors, stators, and coils used in electric motors. This new machine is designed for small to medium production volumes and offers superior insulation, improved performance, and extended operating life for these critical components.
Read more aboutEvents
See all upcoming trade fairs
The Battery Show North America 2025
Productronica 2025
xEV Detroit, USA 2025
Our products - for your individual requirements
With our comprehensive equipment portfolio, we offer process-reliable applications in the fields of dispensing, impregnation, heat staking and plasma.
Our service offer
We offer our customized service worldwide.
Need technical assistance?
Contact our offices in Europe, Asia or North America today.
Europe
Maintenance & Inspection
Create your individual service and maintenance plan with us and increase your plant availability. Our competent specialists analyze the condition of the plant.
Conversions & Retrofits
You want to rebuild your plant and make it fit for the future? Together we will find the best solution for you to modernize your proven bdtronic systems.
Whitepaper
Stator busbar potting
For a major German Tier1 supplier, bdtronic developed a complete fully automated production line for casting the shift ring on a stator (48-volt to 800-volt possible). Read more in our new whitepaper.
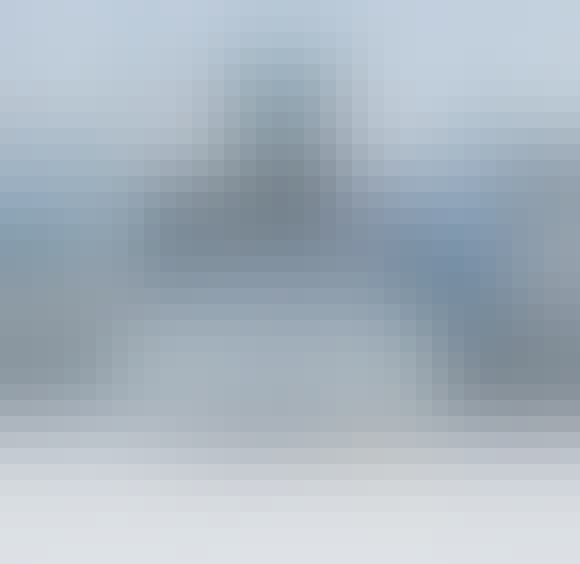
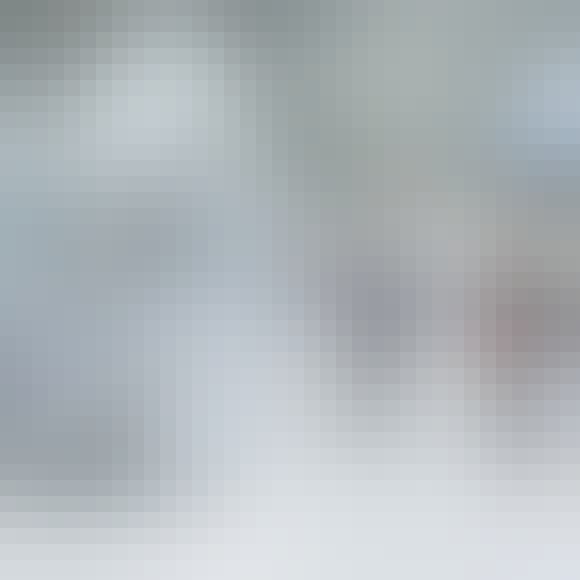
Contact us
Contact us and benefit from our expertise.