The roll dipping impregnation process can be used for both rotors and stators.
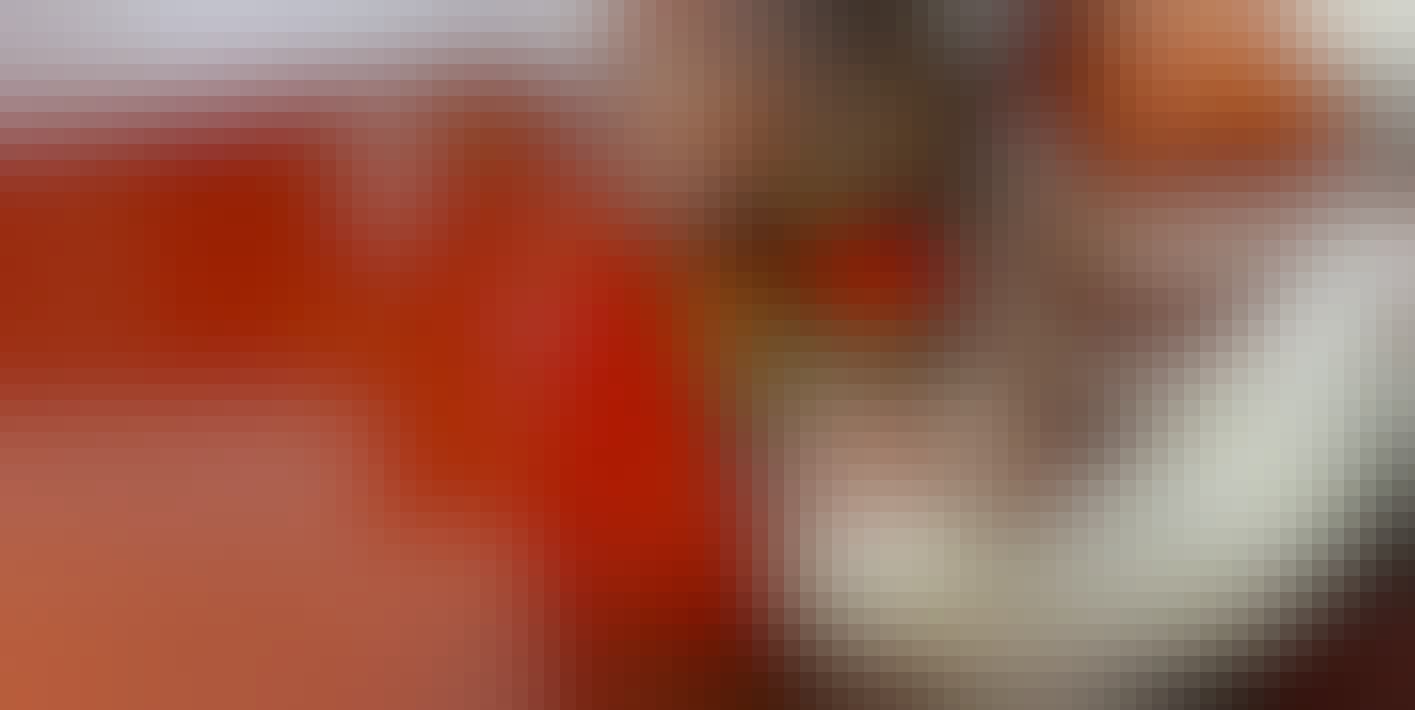
Srcoll
Roll dipping
The roll dipping impregnation process can be used for both rotors and stators. In this process, the components are only partially immersed and rotated in a controlled manner until the desired depth is reached.
Efficient diving
Roll dipping is a further development of the dipping process in which the component is not completely immersed in a basin filled with impregnating resin. The rotors or stators are mounted on special grippers that move with constant rotation around the center axis. In this way, the components are only partially immersed and rotated in a controlled manner until the desired depth is reached. After the component is moved out of the bath, excess material drips back into a collection tray.
The stators or rotors are fixed horizontally on the component holders. These grippers move with constant rotation around the central axis. Mounted here, they are guided through the various processes. The individual processes are preheating, impregnation, gelling, curing and cooling.
In the area of impregnation there are one or more immersion tanks, which optimally regulate the heat. The impregnating resin is located in the dip tanks. When the component to be processed reaches this station, the dip tank automatically moves upwards. Here, the rotor or stator is partially immersed in the resin and then rotated in a controlled manner until the desired depth is reached.
Some advantages of the roll diving method are the following::
- High quality impregnation
- The grooves are filled to the maximum in the windings
- Particularly short process handling
- Maximum productivity for the individual plants
- Perfect coverage and distribution of the resin
- Resins with or without monomers can be used
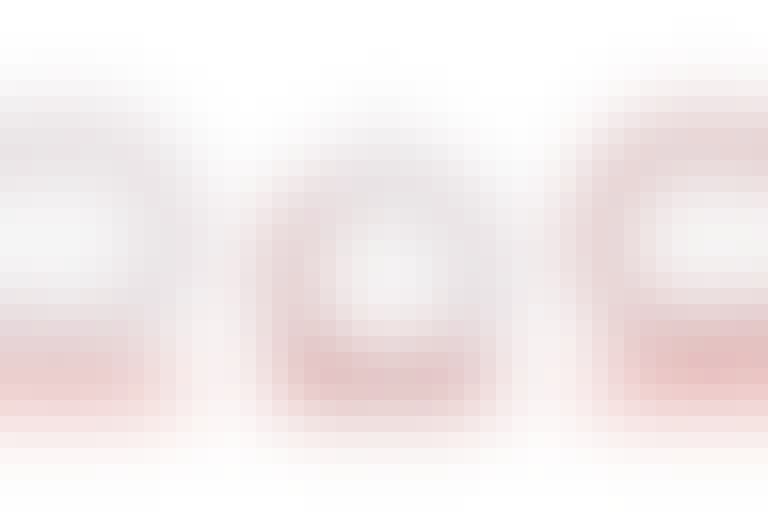
Roll dipping is a further development of the impregnation process dipping, which achieves partial process control.
Technology Center
Benefit from our expertise and many years of experience. Develop the optimum process for your requirements together with us. We are specialists for different applications and processes.
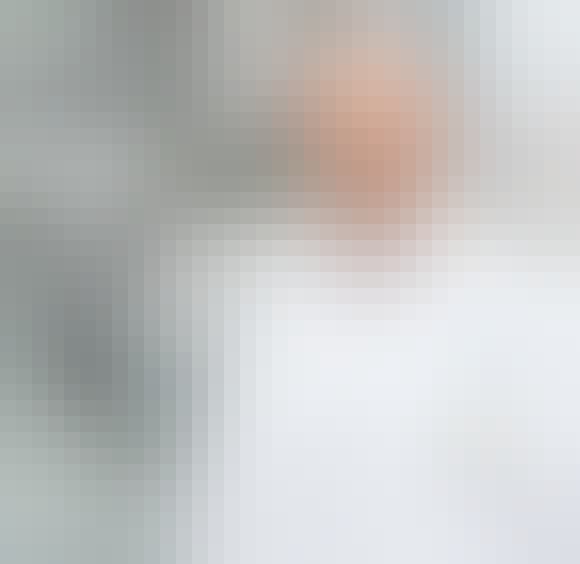