bdtronic has unique process expertise and experience in the impregnation of electric motors for high production volumes.
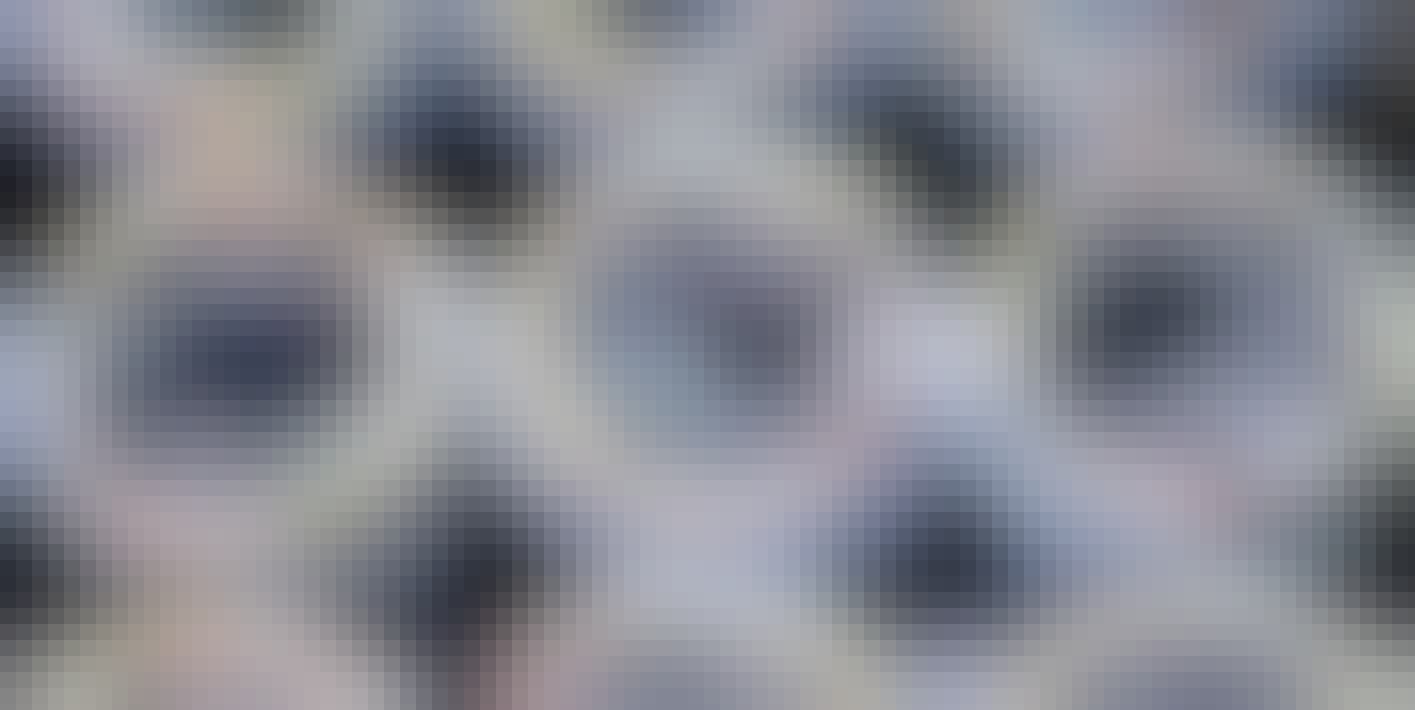
Srcoll
Impregnation technology
Impregnation applications
bdtronic is the leading supplier of impregnation systems for electric motor production.
High quality and reliable
Impregnation is the process of closing and sealing the voids between wires in a component such as an electric drive motor with an insulating material. Impregnation of the electrical windings of rotors and stators in the electric motor, hybrid motor, generator, hydraulic motor, pumps or the coils in transformers or substations improves the overall performance and helps to extend the operating life of the drive train. Resin impregnation of windings and copper wires provides better insulation and prevents damages from vibration. It also improves resistance to thermal stress, increases heat exchange during normal operation, and reduces the risk of short circuits in the windings. Thus, the impregnation process increases thermal conductivity and contributes to a better environmental balance.

Impregnation of stators
Electric drives
bdtronic offers a highly developed impregnation technology for the secondary insulation of stators and rotors of electric motors.
Stator windings
The stator is the main component of every electric motor. bdtronic has the right impregnation equipment for every type of stator winding.
Stator coating
The welding zones of hairpin or I-pin stators must be protected from external influences. bdtronic combines impregnation of the stators with powder coating technology.
Impregnating resins and methods
Learn more about impregnation resins, the appropriate impregnation method and find the right impregnation system for your application.