Robotic solutions: Future production technologies dispensing, plasma and heat stakingres the energy.
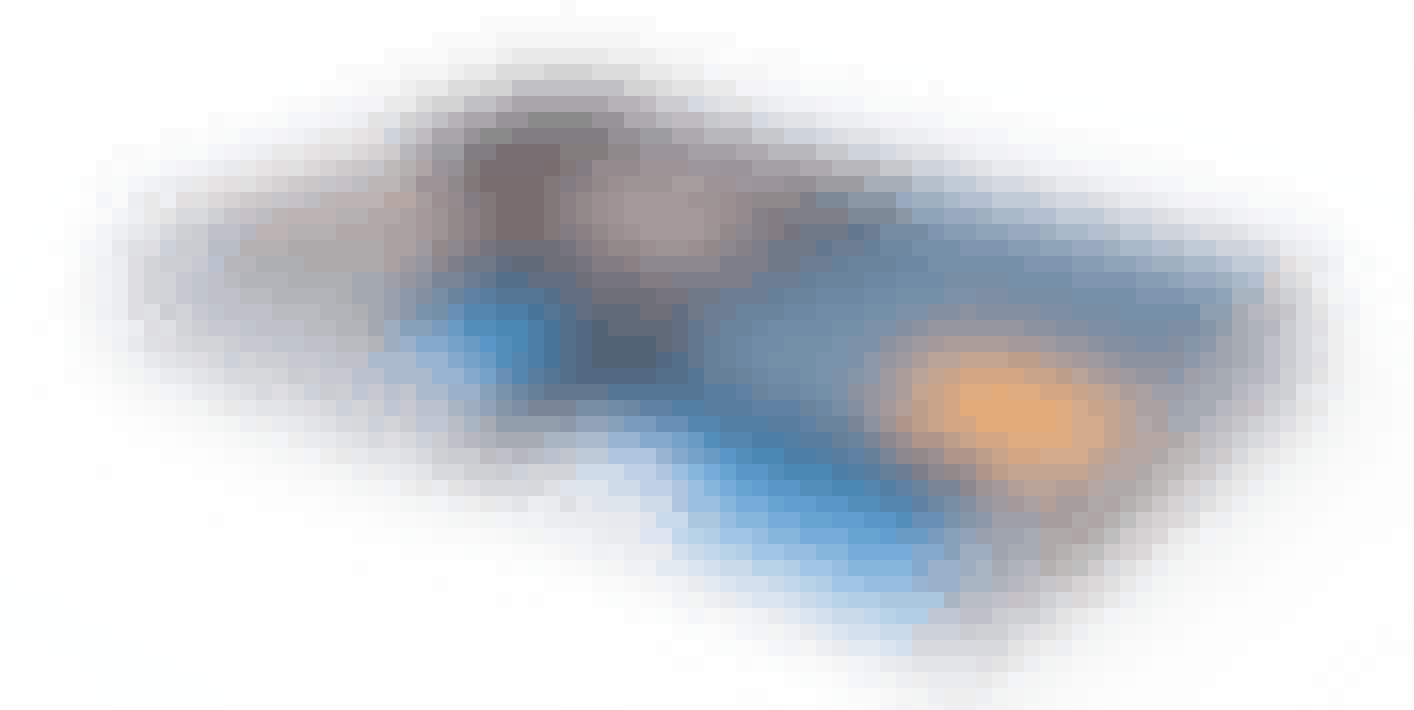
Srcoll
Process solutions for Potting I Thermal Management I Joining
Battery production
Batteries for automotive applications need to be reliable, safe, and high-performing, making them suitable for all needs of mobility.
The heart of the electric vehicle
The battery plays a central role in electric vehicles (EVs), as it serves as the primary power source and energy storage device. This property is of fundamental importance when it comes to increasing the range of electric vehicles and ensuring sufficient mileage per charge for practical use.
Advances in battery technology have led to improved longevity and durability, which increases the overall performance and economic viability of EVs. The environmental impact of EVs is also significantly lower, as they produce no tailpipe emissions during operation thanks to the battery-powered drive system.
Essentially, the role of the battery in the electric vehicle ecosystem goes beyond pure energy storage; it is a catalyst for sustainable transportation and drives innovation towards clean and efficient mobility solutions.
Technologies for batteries
To achieve highest results in reliability, safety and performance, batteries are potted or injected with resin. To avoid thermal runway and propagation foam encapsulation is used. Thermal interface materials are dispensed to dissipate heat from the batteries. For long lasting joints and to fix parts together, joining techniques like heat staking or bonding are used.
Dispensing
Potting applications in batteries
Thermally conductive materials are dispensed in battery packs or potting in battery management systems and many other dispensing processes are used in battery systems.
Applying thermal interface materials to dissipate heat or encapsulation with foam to avoid thermal propagation.
Heat staking
Long-lasting joints for battery packs
Heat staking is the ideal joining technology for sensitive electronic components. There is no need for additional screws, when using plastic materials to join parts in electronics. In battery applications like battery management systems and battery sensors, heat staking is used as a method to join parts of different material, using the plastics of housings.
Plasma
Pre-treatment of surfaces
Before the adhesive is applied, the battery cells are pretreated with plasma to activate and clean the surface. This achieves the best possible and long-term stable adhesion.
High-volume dispensing
bdtronic has developed a system that enables the processing and dispensing of large quantities of gap filler material in the shortest possible time.




Whitepapers about battery applications
Get to know more about the battery production solutions for the technologies plasma, dispensing and heat staking.
Gap filler injection
More efficient battery module manufacturing
How a new gap filler injection process improves pouch-cell module assembly.
JOINING METHODS FOR EV BATTERY PACK APPLICATIONS
Heat staking of flame retardant PP compounds
Study results: bdtronic’s convection and conduction heat staking technologies with SABIC® PP compound H1030.
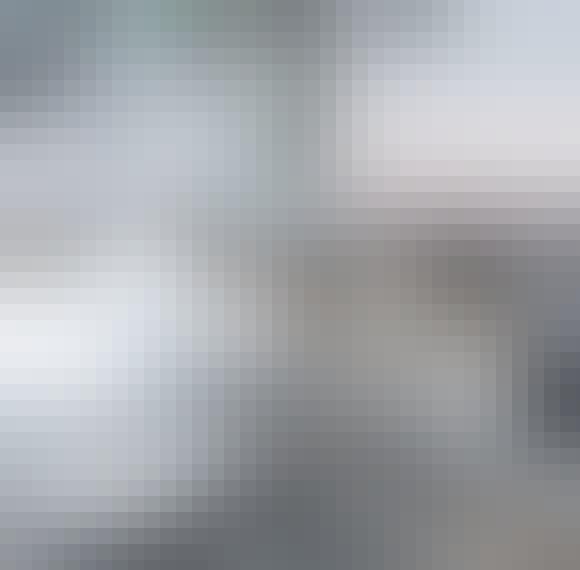
control units for battery and cell management
The optimal joining technique for different materials
Using the battery and cell management system for electric vehicles as an example, the whitepaper presents heat staking of thermoplastics as a joining technique for various materials.
Dispensing thermal adhesive for battery manufacturing of electric cars
Built-in high-voltage (HV) batteries play a major role in electromobility. They are the heart of an electric vehicle and store the energy.










On-Demand webinars about battery production
Process technology for electromobility and power electronics
How to dispense thermal interface materials (TIM) perfectly
Thermal conductive pastes are pasty 1C or 2C media that adapt optimally to the individual contours of the component. Their demanding material properties require special attention in material preparation and dispensing technology.
Heat staking for the automotive industry
Fixing a PCB in a plastic housing
In order to meet the requirements for weight and cost reduction and extended functionalities the use of plastic components in the automotive industry is growing. Autonomous driving and the electrification of the powertrain have increased the number of electronic and sensor products in cars. Each electronic contains a printed circuit board (PCB) and fixing a PCB in a plastic housing by means of heat staking is clean, cost-effective, precise and today state of the art.
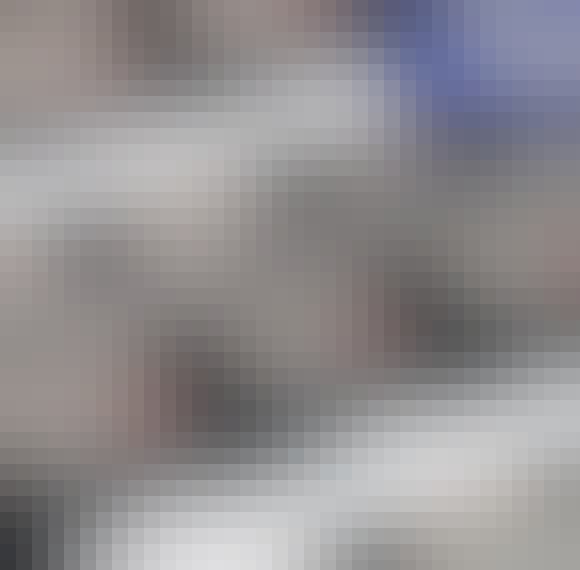

Sealing Cooling Plates in Batteries with Epoxy Resin and speedUP Technology
Events
The Battery Show North America 2025
Productronica 2025
xEV Detroit, USA 2025
The future of mobility is electric! Electromobility is the key to a climate-friendly future and at the same time one of the greatest challenges of our time. Electrically powered vehicles produce significantly less CO2 and thus contribute to climate protection. More and more electric and hybrid vehicles are being registered worldwide.
With our process technologies, we are making our contribution to electromobility. Our dispensing machines, plasma cleaning systems, heat staking and impregnation machines are required for a wide range of applications in the production of hybrid or electric vehicles.