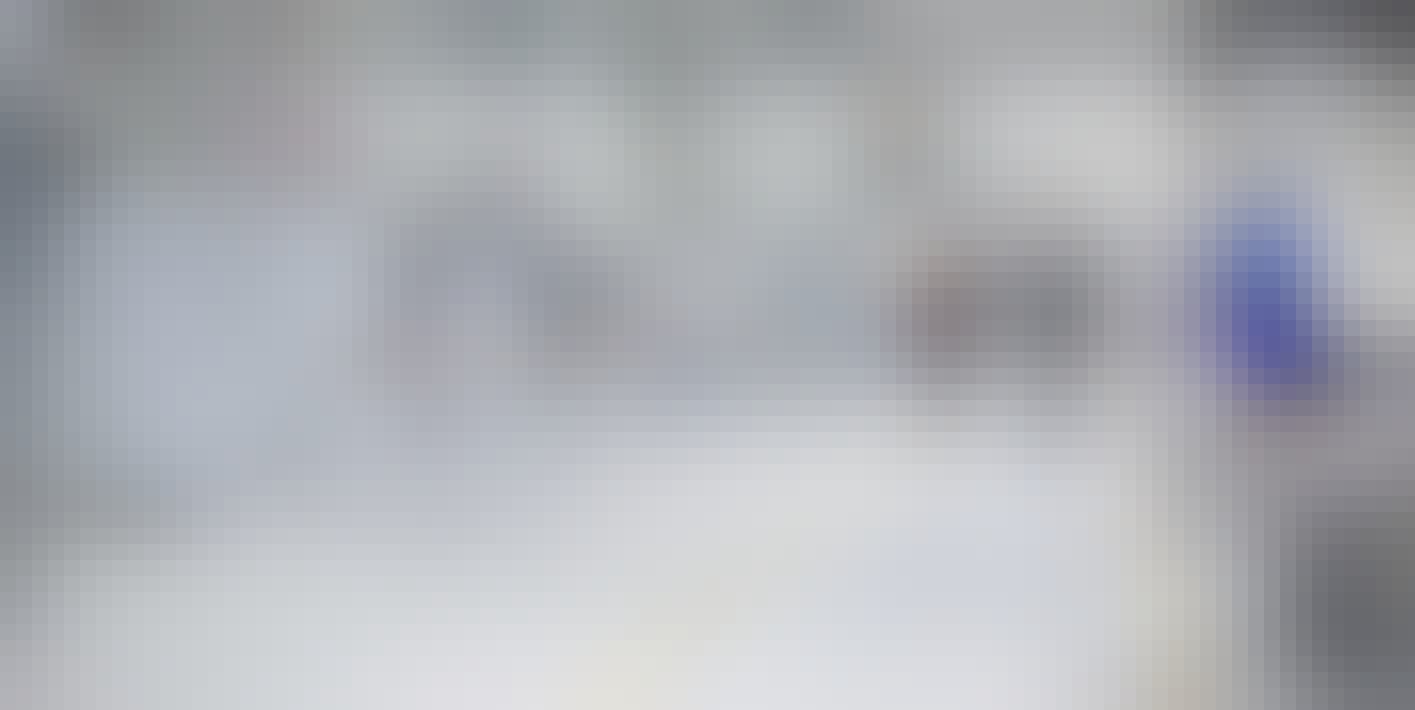
Srcoll
Dispensing machines
Material preparation for highly viscous to pasty materials
The PPS, DPS and CPS material preparation systems are suitable for highly viscous to pasty, high-filler and abrasive materials.
Gentle to material and clean
Material preparation is carried out by removing material from original containers, whereby the sizes of the containers can vary. The container change is clean and uncomplicated, so that hardly any downtimes occur. Optimum residual emptying of the container minimizes material loss. The bdtronic technology offers conveying of the material with lowest conveying pressure. Sedimentation due to e.g. a high conveying pressure is completely prevented.
Moisture-curing adhesives are conveyed through a vacuum chamber. Vacuum degassing with an integrated vacuum control perfectly prepares the potting medium for bubble-free dispensing without residual moisture. Furthermore, variable follower plate sizes are available for a wide range of potting diameters.
PPS
Material preparation for highly viscous to pasty, high-filler and abrasive dispensing materials
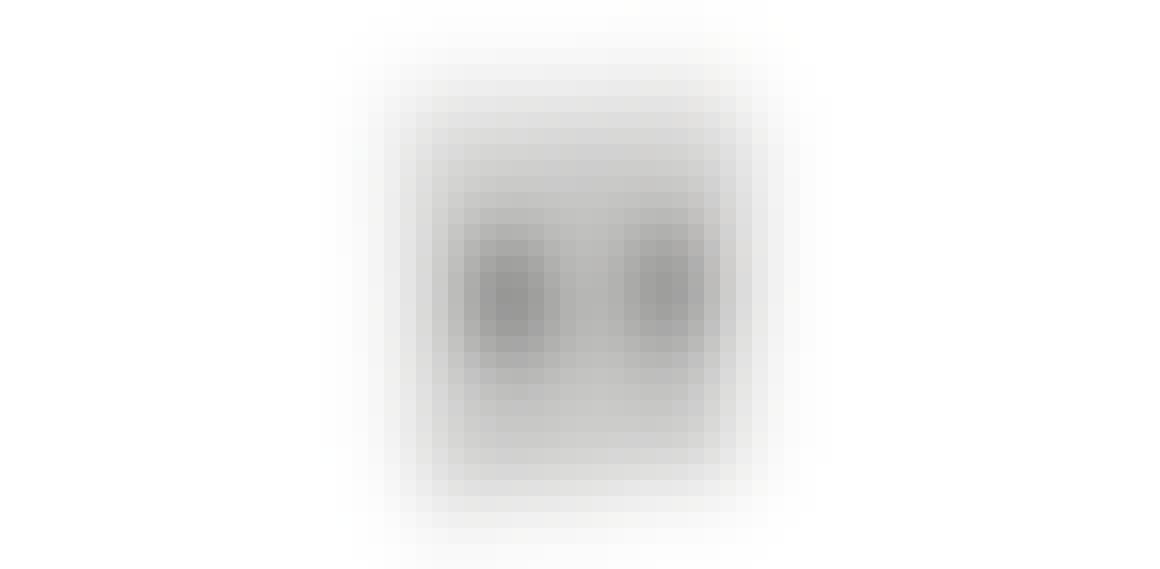
Characteristics
Frame incl. sheet metal enclosure and integrated control cabinet
Signal status light
Conveyor unit
Feed pump design screw pump
Extendable receiving plate for containers
Variable follower plate sizes for a wide range of bundle diameters
Available as a tandem version for uninterrupted production when changing buckets, without production stop
Advantages
Gentle on materials thanks to low working pressures
Analog level monitoring
Low space requirement
Clean and uncomplicated container exchange
Optimal residual emptying
Technical data PPS
1K PPS | 2K PPS | ||
Dimensions (WxHxD) | 670 mm x 1.700 mm x 680 mm | 1.340 mm x 1.700 mm x 680 mm | |
Floor space | < 0,45 m² | < 0,9 m² | |
Weight | 450 kg | 880 kg | |
Electrical power supply | 400 V / 50 Hz 16 A / 32 A fuse protection | 400 V / 50 Hz 16 A / 32 A fuse protection | |
Pneumatic supply | max. 6 bar | max. 6 bar |
DPS
Material preparation for highly viscous to pasty, high-filler and abrasive dispensing materials from large containers
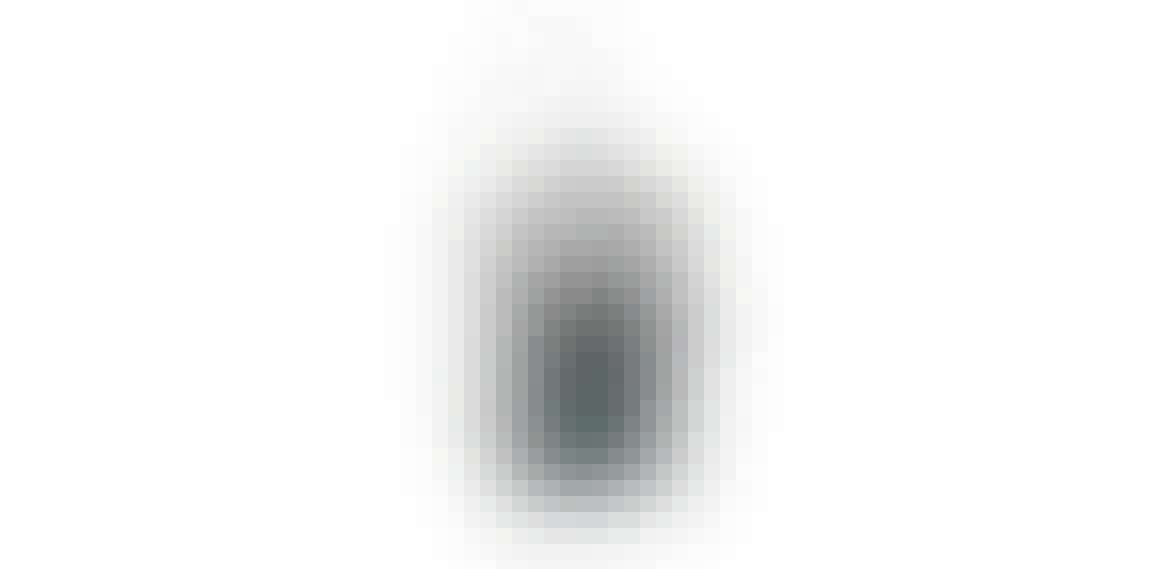
Characteristics
Frame incl. sheet metal enclosure and integrated control cabinet
Separate emergency stop circuit, signal status light
Conveyor unit
Feed pump design screw pump
Analog fill level monitoring
Available as a tandem version for uninterrupted production when changing drums, without production stop
Advantages
Available for 60 l and 200 l drums
Gentle on materials thanks to low working pressures
Minimization of downtimes through use of large containers
Clean and uncomplicated container exchange
Optimal residual emptying
Technical Data DPS
1K DPS | 2K DPS | ||
Dimensions (WxHxD) | 1.210 mm x 3.450 mm x 1.300 mm | 1.210 mm x 3.450 mm x 2.610 mm | |
Footprint 1K DPS | < 1,45 m² | < 2,9 m² | |
Weight | approx. 630 kg | approx. 1,300 kg | |
Electrical power supply | 400 V / 50 Hz 32 A fuse protection | 400 V / 50 Hz 32 A fuse protection | |
Pneumatic supply | max. 6 bar | max. 6 bar |
CPS
Material preparation for highly viscous to pasty, high-filler and abrasive dispensing materials from cartridges
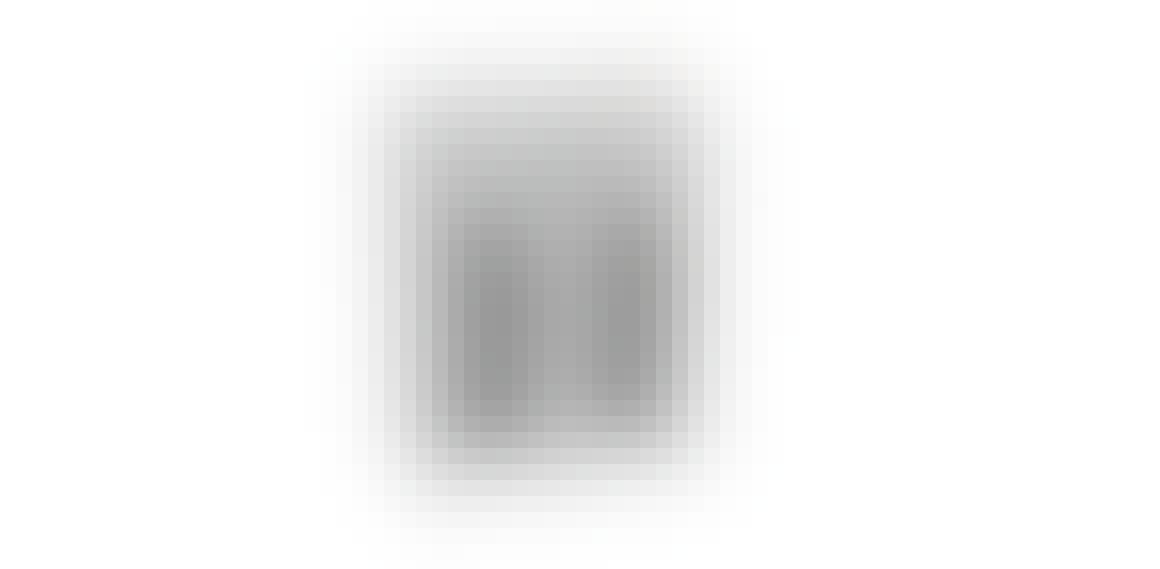
Characteristics
Frame incl. sheet metal enclosure and integrated control cabinet
Separate emergency stop circuit, signal status light
Conveyor unit
Feed pump design screw pump
Analog level monitoring
Advantages
Gentle on materials thanks to low working pressures
Low space requirement
Clean and uncomplicated container exchange
Optimal residual emptying
Technical Data CPS
1K CPS | 2K CPS | ||
Dimensions (WxHxD) | 670 mm x 1.700 mm x 680 mm | 1.340 mm x 1.700 mm x 680 mm | |
Floor space | < 0,45 m² | < 0,9 m² | |
Weight | 450 kg | 880 kg | |
Electrical power supply | 400 V / 50 Hz 16 A / 32 A fuse protection | 400 V / 50 Hz 16 A / 32 A fuse protection | |
Pneumatic supply | max 6 bar | max 6 bar |
Configuration and expansion options
1K or 2K Material preparation
Slave variant for bdtronic dispensing machines
In-house process control
Use as integratable dispensing system
Variable diameter of the follower plates
Suitable for different container heights
DPS vacuum follower plate for bubble-free container changeover
DPS: Fold-out pick-up plate for containers
Membrane drying unit
Barcode scanner for scanning ID material container
Database connection MDE / BDE
ESD equipment
1K dispensing structure
1K dispensing assembly mini-dis (microdispensing)
2K dispensing assembly static for liquid dispensing materials
2K dispensing assembly mini-dis (microdispensing)
2K dispensing structure dynamic
Multi-head applications
Application areas
The dispensing process bonding joins two or more joining partners together.
The dispensing process Sealing is an effective method of protecting components from external influences by creating a barrier.
The application of thermally conductive pastes is used to dissipate heat in order to protect power electronics from reduced performance or defects caused by overheating.